In the push to get more students into college and on career-ready tracks, fewer and fewer high school students are making the jump into one of the industries that employs the most Americans: manufacturing.
But why?
According to David Clayton, director of Greenville Technical College’s Center for Manufacturing Innovation (CMI) in South Carolina, the answer lies in part due to a longstanding, oversimplified stereotype that’s pervaded the industry for years.
“The image a lot of people have of manufacturing is that these jobs are fairly low wage, that workers are in a dirty, dangerous environment, or that the work is dull,” he says. But CMI, Greenville Technical College’s fifth campus, illustrates that manufacturing today is anything but. The multi-million-dollar facility is stocked with today’s most advanced manufacturing equipment ranging from steel 3D printers to precision cutters to collaborative robotics that work alongside humans on the factory floor. Students who enroll in programs at CMI can walk away with an associate degree or certificate training in industrial automation, robotics, mechatronics, engineering design, project management and much more.
As director of the honors college, Clayton spends a lot of time thinking about challenges facing the country’s manufacturing economy—but even more on ways his faculty can buck an outdated image and change the way young people think about modern factory employment. “We are fighting that perception,” he explains.
The facility is part of an initiative that’s now six years in the making. Around 2010, when the U.S. economy began rebounding from the 2008 financial crisis, manufacturers started voicing concerns about finding enough highly-skilled workers. The idea for the facility—and using it to encourage innovation and youth engagement in manufacturing—led to a $25 million bond from Greenville County Council to get plans moving. Additional funding came from community donors and companies themselves, like GE Power, which contributed $500,000.
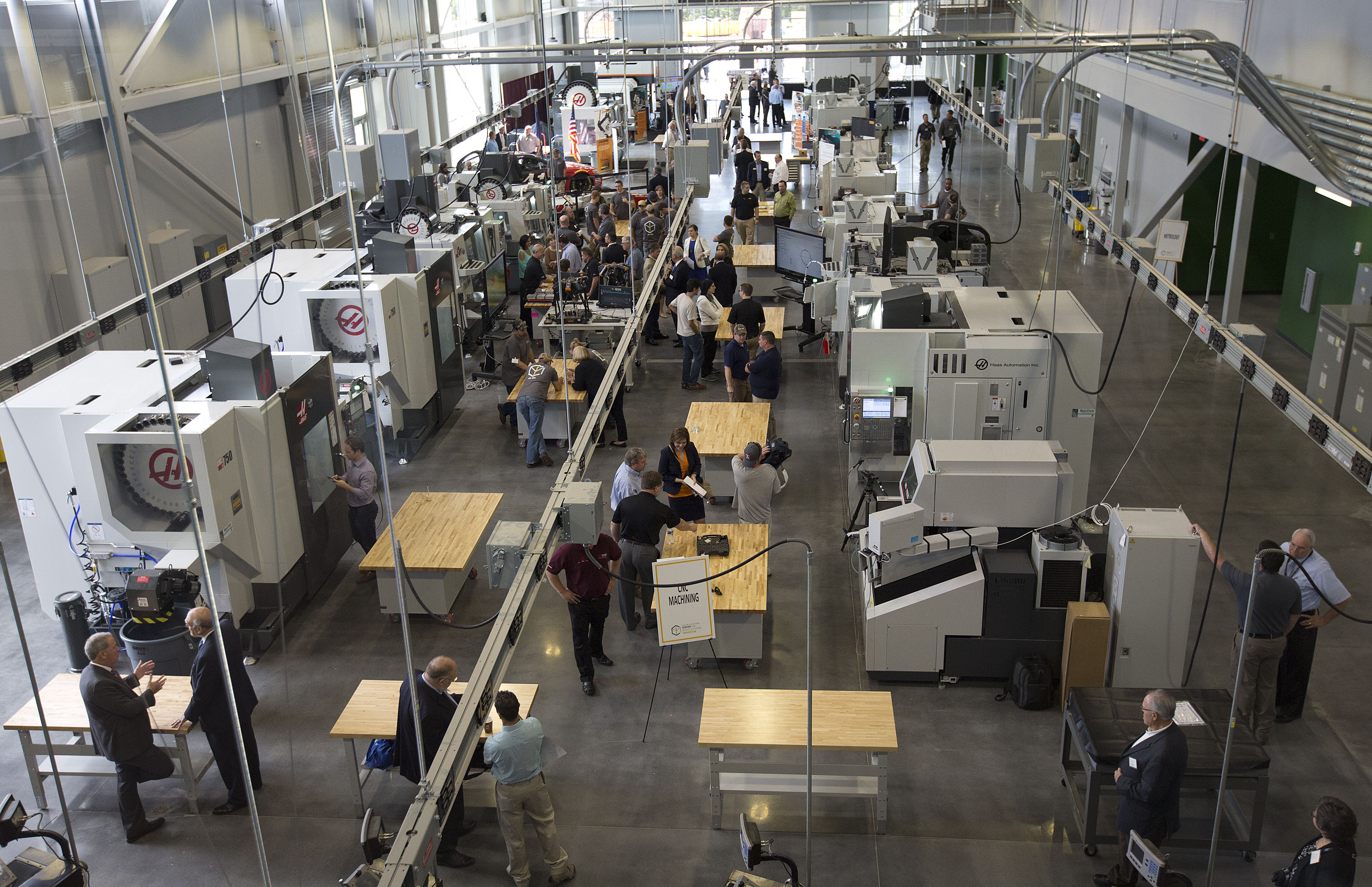
Starting Early
Even in a place like Greenville, South Carolina—a manufacturing powerhouse that exported $28.90 billion in goods in 2014—employers struggle to find high-skilled employees they need to operate, program and build factory equipment. To change that, Clayton and other faculty at CMI are starting early—with high schoolers, that is. “Most high school students have no idea of what manufacturing is,” he says. “The idea to build this facility is to attract more people to these careers.”
Since opening its doors in September 2016, CMI regularly hosts field trips for students to see the kinds of learning and technology Greenville offers. A must-stop on any tour is the facility’s Bridge to Learning, where guests can look down through the glass floor to see some of the facility's machinery and research in-progress. “[The bridge] gets a lot of ohs and ahs,” Clayton says.
For students and classrooms that can’t make it to the college campus, CMI faculty makes trips to visit high schools and try to get students interested manufacturing. “We talk a lot about robotics with youth because robots can really tweak their interest,” says Rodney Jones, director of mechatronics at CMI. “Then we shoot the conversation back to things they are more familiar with, like little push cars or the clock in their room. We tell them that’s all automation, and that’s what we teach.”
A former floor technician for Michelin, Jones has watched the manufacturing industry evolve over the last 20 years. “In the past, we were on the floor 24/7, there were a lot of screwdrivers and you were working,” says Jones. “That’s not all that it is anymore. You can go in as a robot programmer or a computer technician. You work clean and come home clean.”
In addition, the average salary for manufacturing workers with an associates degree in Greenville County is about $64,000. Yet despite those opportunities, Jones says another question frequently pops up when talking to young people about the profession: Aren’t robots replacing factory jobs?
Not yet, according to Jones, who also meets with companies to find out their manufacturing needs and keep CMI curriculum in line with market demand. “The more robots there are, the more people we need to train them and make them work,” he tells students. “We need robot programmers, and that’s what the companies are really looking for on the factory floor.”
In Jones’ department, students are preparing for these jobs by learning how to control the robots that assemble things like cars or textiles. “We program them using numbers and letters. Say, AO47, that will represent a parameter to tell the motor to speed up or slow down,” Jones explains. “You can put in different parameters to do different things like start, stop, go again, reverse—whatever you want.”
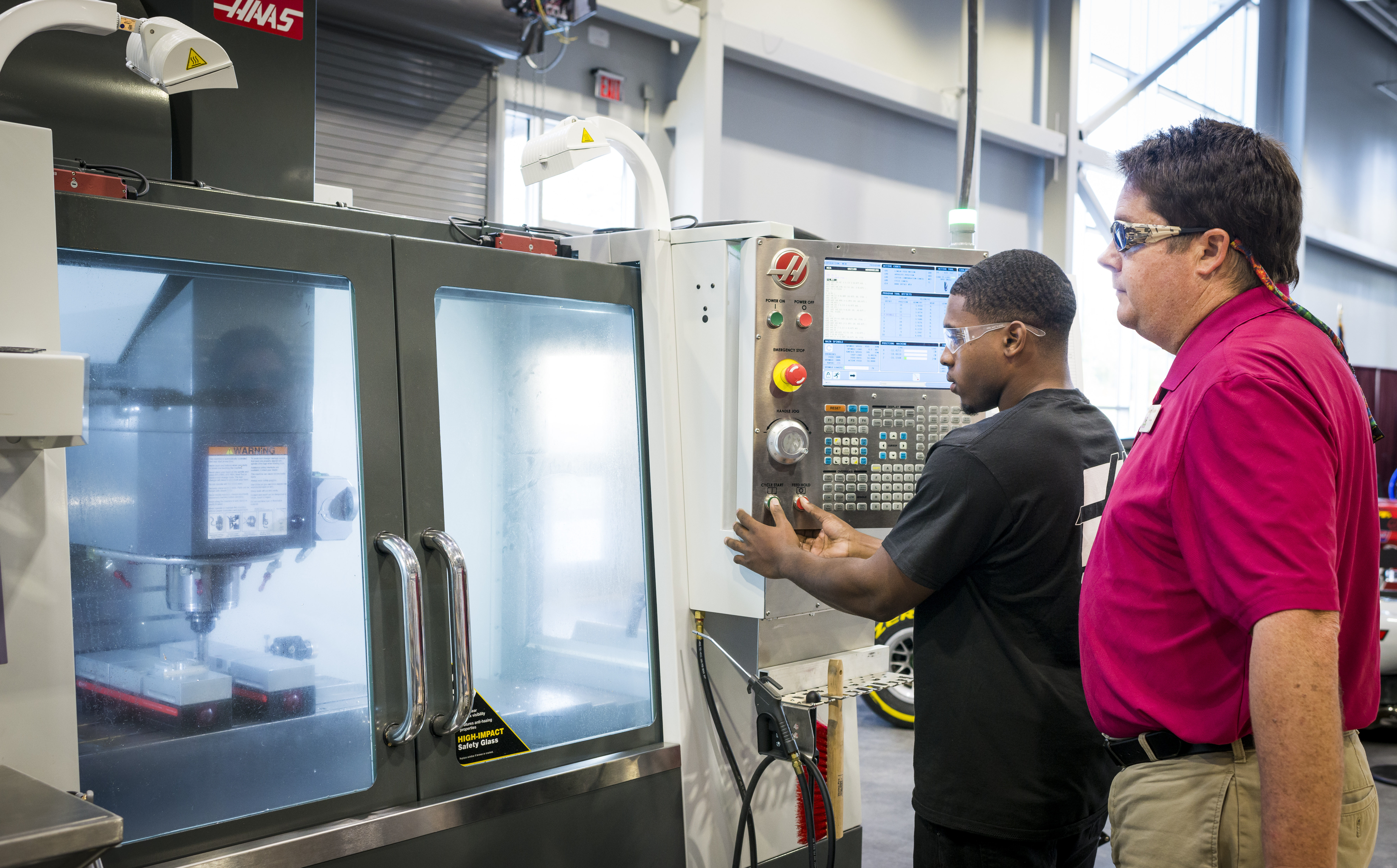
Company and College Collaboration
While exposing kids to what manufacturing jobs can look like today, CMI is also working to change the manufacturing industry from within. Through a collaboration with Clemson University—the first integrated education partnership between a technical college and research institution in the U.S.—the center is connecting engineers with technicians before they enter the workforce.
“Quite often, the engineer doesn’t have a clear understanding of the manufacturing process, and the technician isn’t well versed in design concepts,” Keith Miller, president of Greenville Technical College, said in a prepared statement. “A solution to this gap at CMI is in bringing the education of the technician and that of the engineer together so that by the time they enter the workplace, they have already learned from one another in a project-based environment, and they are ready to team up again on the job.”
Along with its partnership with Clemson, CMI also partners directly with employers to offer corporate training and continuing education. For instance, BMW recently sent 13 of its employees to CMI for a 10-week long course. Instead of showing up for work at BMW’s manufacturing plant—located just 12 miles away from CMI—workers head to Greenville for 40 hours a week to be trained in the concepts that Clemson and Greenville students typically learn over the course of their associates or bachelors degree programs.
With enhancements—like informational touch screens, an augmented reality viewer and an exploration touch station for visitors—still in the works at CMI, the facility and its director are also stepping in to help the government with its own advanced manufacturing initiative. A $253 million project largely funded by the Department of Defense, the Advanced Robotics Manufacturing Institute (ARM) will be used to study and further develop new technology around manufacturing, artificial intelligence, 3D printing and robotics. Nearly 84 industry partners, 35 universities and 40 other groups across the country are working on the project, which will be based in Pittsburgh, Pennsylvania near university partner Carnegie Mellon.
Last December, a White House report pointed out the dangers of job loss as automation increases in the country’s manufacturing industry, and the need for a “stronger social safety net to help workers who will eventually be displaced by robots in the coming years,” Recode reports. With the help of CMI—which will run one of the ARM’s eight regional robotics collaboratives—ARM is aiming to offset that potential job loss with a goal of creating 510,000 new manufacturing jobs in the U.S. in the next 10 years.